How Shock Absorbers Ensure a Safer Working Environment in Factory Settings
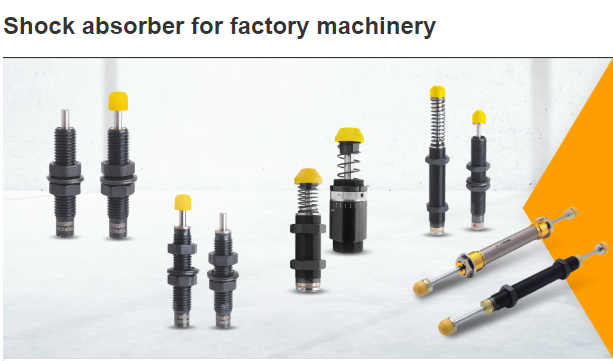
Safety in factory settings is of utmost importance in today’s industrial landscape. Amidst various factors influencing workplace safety, shock absorbers emerge as crucial. These devices play a pivotal role in creating a secure work environment by reducing the risks tied to machinery accidents.
Shock absorbers significantly enhance factory safety with their adept capacity to counteract and dampen hazardous forces. This article explores how shock absorbers safeguard personnel and machinery, highlighting their importance in promoting a safer and more productive industrial workspace.
How Does Shock Absorber Reduce The Risk Of Machinery-Related Accidents And Injuries
Shock absorbers ensure a safer workplace by minimizing dynamic force impact, stabilizing equipment, dampening vibrations, improving operator control, and safeguarding machinery and workers. These significantly reduce the risk of machinery-related accidents and injuries through several key mechanisms:
Absorbing Impact Energy
One of the primary shock absorbers features is to absorb impact energy. When machinery experiences sudden impacts or forces, shock absorbers act as a buffer by absorbing a substantial portion of the energy generated during the impact. This energy absorption cushions the force of impact and prevents the abrupt transmission of energy to nearby equipment or personnel. By doing so, they effectively reduce the severity of jolts, preventing sudden and unexpected movements that can lead to accidents. This mechanism is particularly valuable in scenarios where machinery needs to come to an abrupt stop or encounters unexpected collisions.
Dampening Vibrations
Vibrations are inherent in machinery operations and can adversely affect equipment and workers. Prolonged exposure to vibrations can lead to discomfort, fatigue, and even health issues for workers. This challenge is addressed through shock absorber damping. They absorb and dissipate the energy generated by vibrations, resulting in a more controlled and stable operational environment. This controlled environment reduces the risk of accidents stemming from uncontrolled machinery movements caused by excessive vibrations.
Stabilizing Equipment
Sudden and jerky machinery movements can catch operators off guard, leading to accidents and injuries. These play a crucial role in stabilizing equipment movements. They slow down and stabilize sudden movements by providing controlled resistance, allowing operators to anticipate and respond effectively. This stability reduces the likelihood of operators losing control or balance due to unexpected shifts in machinery motion. As a result, they prevent accidents caused by operator disorientation during unexpected machinery movements.
Enhancing Operator Control
A smoother operational environment enhances operator control over machinery. They create this environment by ensuring that movements are controlled and predictable. With improved control, operators can avoid sudden and jerky movements that might otherwise lead to accidents. This heightened control allows operators to maneuver equipment more efficiently and reduces the likelihood of human errors caused by abrupt machinery actions.
Protecting Personnel
The protection of personnel is of paramount importance in any industrial setting. They serve as a protective barrier between machinery and workers. In scenarios where machinery encounters sudden impacts or movements, they absorb and dissipate the forces generated by these events. This absorption prevents the transmission of excessive forces to workers, thereby mitigating the risk of injuries caused by machinery-related impacts. This protective function is particularly crucial in environments where workers are in close proximity to heavy machinery, and potential accidents can result in severe injuries.
Prolonging Equipment Life
The durability and longevity of machinery are essential for sustained operations. Excessive forces and impacts can accelerate the wear and tear on machinery components, leading to increased maintenance needs and potential equipment failures. They play a pivotal role in preserving equipment life. By absorbing and dissipating forces before they reach critical equipment parts, shock absorbers reduce the stress placed on machinery components. This preservation of equipment integrity minimizes the risk of machinery-related failures that could lead to accidents.
Why Should Factory Companies Invest To Shock Absorbers
Investing in shock absorbers aligns with worker well-being, efficient operations, and overall business success. Addressing machinery-related risks proactively creates a safer, more productive industrial environment. Factory companies should invest in shock absorbers for nine compelling reasons:
- Enhanced Workplace Safety
The foremost reason is the improvement of workplace safety. Shock absorbers effectively mitigate dynamic forces, dampen vibrations, and stabilize equipment movements, significantly reducing the risk of machinery-related accidents and injuries. By investing in these products, companies prioritize the well-being of their workforce and create a safer environment.
- Reduced Downtime
Accidents and equipment damage due to uncontrolled forces can result in downtime for repairs and maintenance. These minimize wear and tear on machinery components, extending their lifespan and reducing the frequency of breakdowns. This translates into decreased downtime, increased operational continuity, and higher productivity.
- Lower Maintenance Costs
Constant repairs and replacements due to machinery wear can lead to substantial maintenance expenses. These act as protective buffers, absorbing impacts and minimizing stress on machinery components. Companies can save on maintenance costs by prolonging equipment life in the long run.
- Improved Operational Efficiency
Stable machinery operation enhances overall efficiency. These contribute to smoother, controlled movements, enabling operators to work more effectively. This leads to improved production processes and streamlined operations, ultimately boosting productivity.
- Regulatory Compliance
Many industries are subject to strict safety regulations and standards. Investing in these products demonstrates a commitment to compliance with these regulations, ensuring that the workplace aligns with industry best practices and avoids potential penalties.
- Worker Morale and Productivity
An environment that ensures the safety and well-being of employees has a positive effect on their morale and productivity. When workers perceive that their safety is a priority and they are shielded from harm, their motivation and involvement in their responsibilities tend to increase. This can result in elevated job satisfaction, reduced employee turnover, and improved overall operational effectiveness.
- Positive Brand Image
Companies prioritizing safety and investing in technologies like these project a positive brand image. Customers, clients, and partners are likelier to trust and engage with companies that are committed to worker safety and responsible operations.
- Risk Management
By reducing the risk of accidents and injuries, companies effectively manage potential liabilities and associated costs. This includes expenses related to medical bills, worker compensation claims, and legal actions resulting from workplace accidents.
- Long-Term Savings
While there is an upfront cost to investing in these products, the long-term benefits far outweigh the initial expenditure. Reduced downtime, lower maintenance costs, improved productivity, and enhanced worker satisfaction all contribute to significant cost savings over time.
Factors to Consider in Buying Shock Absorbers
When buying shock absorbers, several crucial factors should be taken into consideration to ensure optimal performance and value:
- Application Compatibility
Choose shock absorbers designed explicitly for the intended application. Consider factors like the type of machinery, the expected forces, and the operational environment to ensure a proper fit.
- Load Capacity
Determine the maximum load it must handle. Select with a load capacity that matches or exceeds the anticipated forces to ensure adequate energy absorption.
- Force Damping
Different shock absorber brands offer varying levels of force damping. Consider the level of damping required based on the machinery’s movement characteristics and the desired degree of impact cushioning.
- Adjustability
Some offer adjustable damping settings, allowing you to fine-tune the resistance level. This can be beneficial in scenarios where machinery requirements change over time.
- Installation and Mounting
Ensure that they are compatible with the mounting points on the machinery. Consider factors like size, shape, and mounting mechanism to ensure a secure and efficient installation.
- Durability and Lifespan
Look for shock absorbers constructed from high-quality materials that can withstand operational demands and potential environmental factors. A longer lifespan reduces maintenance and replacement costs.
- Vibration Dampening
If vibration control is a priority, opt for a brand that dampen vibrations. Consider the frequency and magnitude of vibrations generated by the machinery.
- Maintenance Requirements
Evaluate the shock absorber maintenance needs. Some may require periodic checks or replacements, while others might be more maintenance-free.
- Temperature and Environmental Considerations
Factor in the operating environment’s temperature range and conditions. Some may have limitations in extreme temperatures or corrosive environments.
- Budget
Balance the desired shock absorber features and quality with your budget constraints. While investing in reliable is essential, finding the right balance between cost and performance is essential.
- Manufacturer Reputation
Choose reputable manufacturers known for producing high-quality shock absorber types. Reading reviews, seeking recommendations, and researching the manufacturer’s history can provide insights into their reliability.
- Warranty
Verify the warranty provided by the manufacturer. A lengthier warranty duration frequently indicates the manufacturer’s assurance in the product’s durability and effectiveness.
- Installation and Technical Support
Consider the availability of technical support and installation assistance from the manufacturer or distributor. Adequate guidance can ensure proper installation and optimal performance.
Empowering Industrial Safety with Misumi
Integrating shock absorbers into factory settings is more than a technological enhancement; it’s a strategic decision that enhances safety, efficiency, and overall business prosperity. By harnessing the protective capabilities of shock absorbers, factory companies lay the foundation for a secure, productive, and sustainable industrial workspace. As industrial operations continue to evolve, the significance of shock absorbers in ensuring a safer and more efficient future remains steadfast.
Elevate workplace safety and performance with MISUMI’s premium shock absorbers Enhance protection for both machinery and personnel by incorporating flexible shaft couplings that safeguard equipment from damage, accommodating minor misalignments, vibrations, and shocks between interconnected shafts. Discover our pioneering solutions at the nexus of precision, dependability, and ingenuity. Step into the realm of advanced workplace safety and productivity with MISUMI.