Guardians of Quality: The Role of Wiring Harness Manufacturers in Delivering Uncompromising Excellence
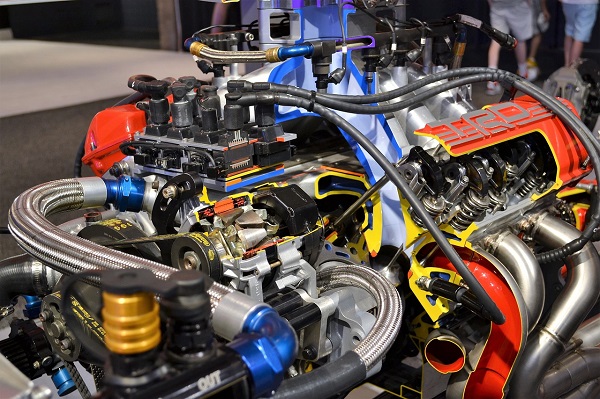
In the intricate and ever-evolving world of modern technology, wiring harnesses stand as unsung heroes, silently ensuring the seamless flow of power and information. Behind every functional electronic device, from automobiles to appliances, lies the expertise of wiring harness manufacturers. These dedicated artisans are the guardians of quality, weaving together intricate networks of wires, connectors, and components to create the lifelines of our technological age.
The Crucial Role of Wiring Harnesses
Wiring harnesses, often referred to as cable assemblies or wire looms, serve as the nervous system of various devices and machinery. They are responsible for transmitting electrical signals, power, and data between different components, enabling devices to function with precision and reliability. This foundational role makes wiring harnesses indispensable in industries such as automotive, aerospace, electronics, and healthcare.
The Artistry of Wiring Harness Manufacturing
Manufacturing wiring harnesses is a delicate art that requires a unique blend of craftsmanship, engineering, and technology. Here’s a glimpse into the intricate process:
1. Design and Engineering
Every wiring harness begins with a meticulous design phase. Engineers create detailed schematics and layouts, considering factors such as component placement, signal integrity, and thermal management. This phase lays the groundwork for a harness that is not only functional but also optimized for efficiency and durability.
2. Component Selection
Wiring harness manufacturers carefully select each component, from wires and connectors to terminals and insulating materials. Components must meet stringent quality standards to ensure optimal performance and longevity.
3. Precision Assembly
The assembly process is a symphony of precision. Skilled technicians meticulously route, bundle, and secure wires, ensuring that they are organized and protected from environmental factors. The delicate balance of achieving both structural integrity and flexibility is a hallmark of expert craftsmanship.
4. Testing and Quality Assurance
Before a wiring harness leaves the manufacturing facility, it undergoes rigorous testing. Automated equipment and manual inspections verify continuity, insulation integrity, and connector functionality. Quality assurance protocols guarantee that each harness meets or exceeds industry standards.
5. Customization and Innovation
Wiring harness manufacturers often collaborate closely with their clients to develop custom solutions tailored to specific applications. This collaborative approach encourages innovation and the development of cutting-edge technologies.
Guardians of Quality: Ensuring Reliability and Safety
The significance of wiring harness manufacturers goes beyond mere assembly; they are the guardians of quality, ensuring the reliability and safety of the end product. The consequences of a faulty wiring harness can be severe, ranging from minor malfunctions to catastrophic failures. As such, manufacturers prioritize uncompromising excellence at every stage of production.
Driving Innovation and Progress
In an era of rapid technological advancement, wiring harness manufacturers play a vital role in driving innovation. As industries demand higher performance, increased efficiency, and enhanced connectivity, manufacturers rise to the challenge. They explore new materials, refine manufacturing techniques, and embrace automation to meet the evolving needs of the market.
Conclusion
Wiring harness manufacturers are the unsung heroes behind the scenes, enabling the functioning of devices that define our modern lives. Their commitment to uncompromising excellence, attention to detail, and innovative spirit make them true guardians of quality. As we navigate the ever-expanding landscape of technology, let us acknowledge and celebrate the indispensable